Power Plant Performance and Efficiency Evaluation
Whether operating modern Combined Cycle, or Fossil Fuel Power Plant, current business and operational requirements pose significant challenges. Maximising performance efficiency and revenue, alongside increasing energy demands, deregulation, raising fuel costs, peak-load generation, environmental constraints, and the mitigation of carbon emissions is key to your business success.
“Are you aware of the wasted energy and loss in monetary revenue in your Power Plant”
“Do you know you can experience losses amounting into the ‘millions’, due to overlooked or neglected seemingly small losses in Plant Performance? You can boost your power plant efficiency to the highest level and prevent these losses.”
We offer a fully flexible consultancy service combining the use of complex system performance software, aligned with plant system and operational expertise to provide significant proven benefits.
Understanding the influence of individual plant equipment function on the overall system performance, is essential for optimizing operation and maintenance activities.
By configuring an identical virtual model of your Power Plant, our Engineers can predetermine real Plant characteristic responses by varying system conditions (Figure 1).
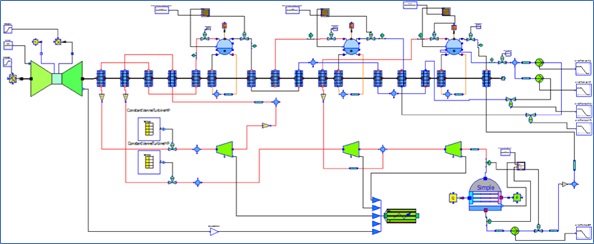
Figure 1: Combined Cycle Power Plant Model
From this virtual power plant model, the system software allows Owners and Engineers to pre-empt reactions to system changes. Working with data supplied by your own operations and maintenance teams, current operating values and performance can be compared with plant design specification and commissioning values, for each individual plant component throughout the thermal system, against which and by comparison plant equipment degradation analysis can be conducted and values determined and data presented (Figure 2).

Figure 2: Contribution of Plant Item Equipment to the Overall Power Degradation
The renewal of Power Plant component equipment can result in unnecessary financial expenditure, and the performance of ageing component equipment can vary significantly when considering the full plant system.
By system modelling, PP system and sub-systems analysis can be performed, to illustrate individual equipment contributions to overall plant performance, and from which condition and degradation deviations can be determined (Table 1).

Table 1
From sample analysis it can be demonstrated how possible performance objectives and rehabilitation scenarios can aid improved plant performance and efficiency.
- The system software enables evaluation of the overall power plant cycle and for each individual plant component throughout the full thermal system
- ‘Off-design’ operating regimes and equipment conditions can be simulated under various ambient and operational conditions
- Upgrade and retrofit plant equipment options can be calculated and the effects of changes predicted
- Extensive ‘what-if’ scenarios and parametric variable studies can be carried out
- Expected performance under various ambient conditions can be computed from the PP model
- Equipment degradations can occur over extended periods and go unnoticed, the analysis can identify and quantify degradation (Figure 3).
- Plant Outage success can be analysed by performing comparison ‘before-and-after’ Plant Outage Overhaul Evaluations (Figure 4)
A system sensitivity analysis can be performed to illustrate the system and sub-system contributions to overall plant performance, and from sample analysis it can be demonstrated how possible performance objectives and rehabilitation scenarios can aid improved plant performance and efficiency (Table 2).

Table 2
Improved efficiency and cost benefit analysis of various rehabilitation options can be demonstrated, to prove the recommended best options (Table 3).

Table 2
Figure 3. Gas Turbine – Expected and Actual Output and Corrected Power Output after an Overhaul
“Your Power Plant Equipment may require unknown maintenance, and over time, malfunctioning equipment will return as material losses”
With our experience we can help and guide operators to adopt an appropriate approach and methodology and prevent unnecessary overspend. Plant ageing brings with it the onset of slow process of equipment degradation and falling efficiency, which can be overcome by correct monitoring and analysis, reducing the risk of failure and consequential breakdown. We can help you to reduce the over-spend, lower the production cost, reduce pollution and at the same time increase profitability.
Training
Power Generation plants operate based on the laws of thermodynamics, and plant performance parameters are calculated based on these laws.
…it is a daunting reality that many plant operators are working with limited knowledge of the laws of thermodynamics.
We also provide training to raise awareness within your operational team to thermal performance, with the aim to optimise the efficient operation of plant.